
Resource Recycling
The Group aims to achieve resource circulation across the entire supply chain by efficiently developing and producing a diverse range of products from limited resources without waste, while promoting recycling to reduce environmental impact.
Sustainable Copper Vision
In August 2022, the JX Advanced Metals Group formulated our Sustainable Copper Vision. This vision reflects our recognition that copper is an essential material for achieving carbon neutrality and describes our policy for the supply and ongoing evolution of sustainable copper.
Green Hybrid Smelting Achieves Dual Missions
We offer copper products using Green Hybrid Smelting. Both copper concentrates and scrap can be used as raw materials. The heat generated by the copper concentrates itself can be used to melt recycled materials, making fossil fuels virtually unnecessary.
Green Hybrid Smelting has been selected as one of the 26 most noteworthy examples of Japan's circular economy initiatives in Case Studies (2022) published by the Japan Partnership for Circular Economy, which was established by the Ministry of the Environment, the Ministry of Economy, Trade and Industry, and Keidanren.
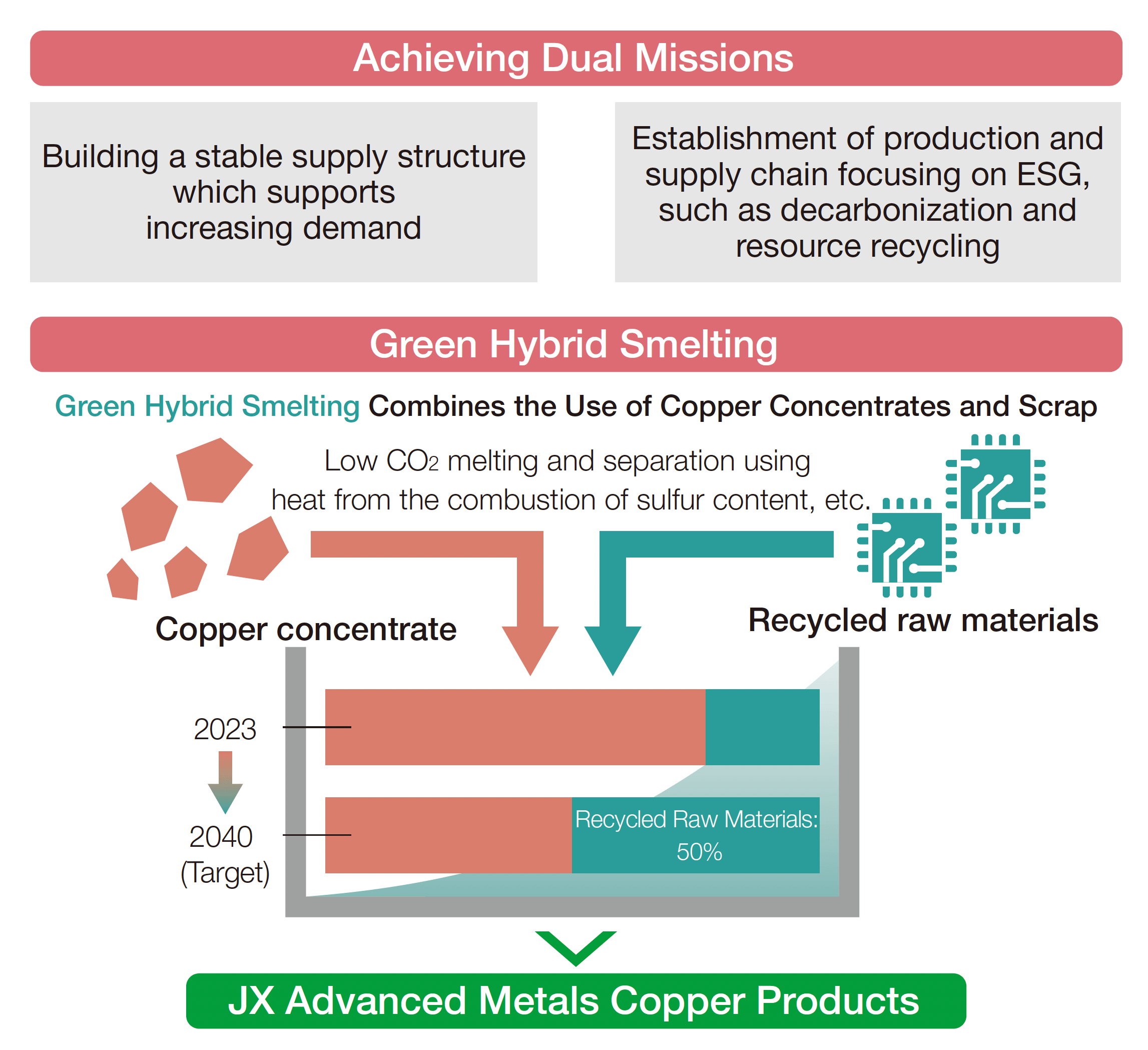
Four Key Initiatives to Develop and Disseminate Sustainable Copper
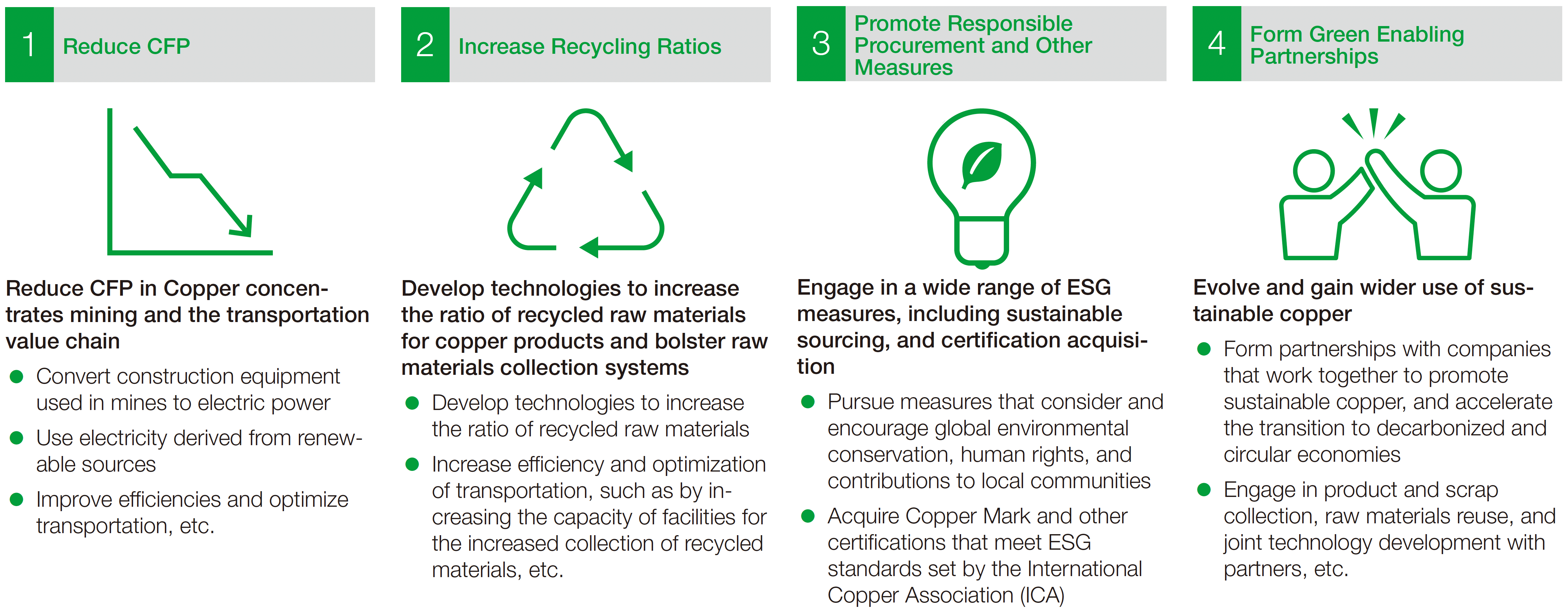
Reduce CFP
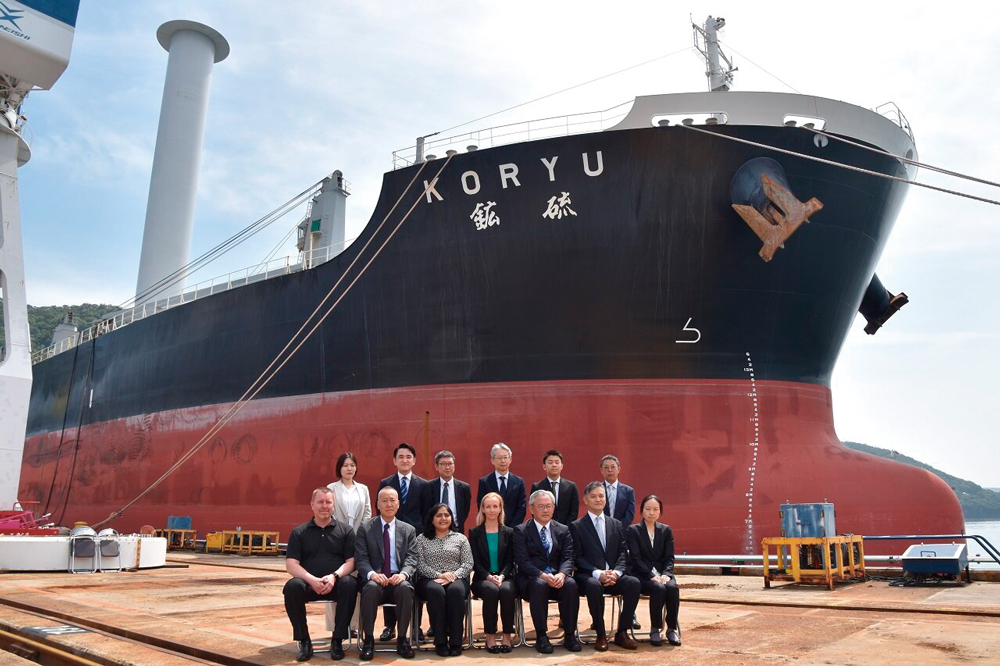
The Group is promoting a joint decarbonization project with the leading mining company BHP Group Limited and wind power propulsion auxiliary equipment manufacturer Norsepower Oy, Ltd. to install rotor sails on the KORYU, an ore and sulfur carrier. Rotor sails are a type of ship propulsion mechanism that uses the Magnus effect to convert pressure differences generated by the rotating cylinders on the hull into dynamic lift. We expect this mechanism to reduce CO2 emissions by 5% as a result of fuel savings.
In July 2024, the installation of the rotor sails was completed and the vessel began its voyage. Moving forward, we will verify the fuel reduction effect and explore further CO2 emission reduction measures.
Increase Recycling Ratios
Green Hybrid Smelting Roadmap
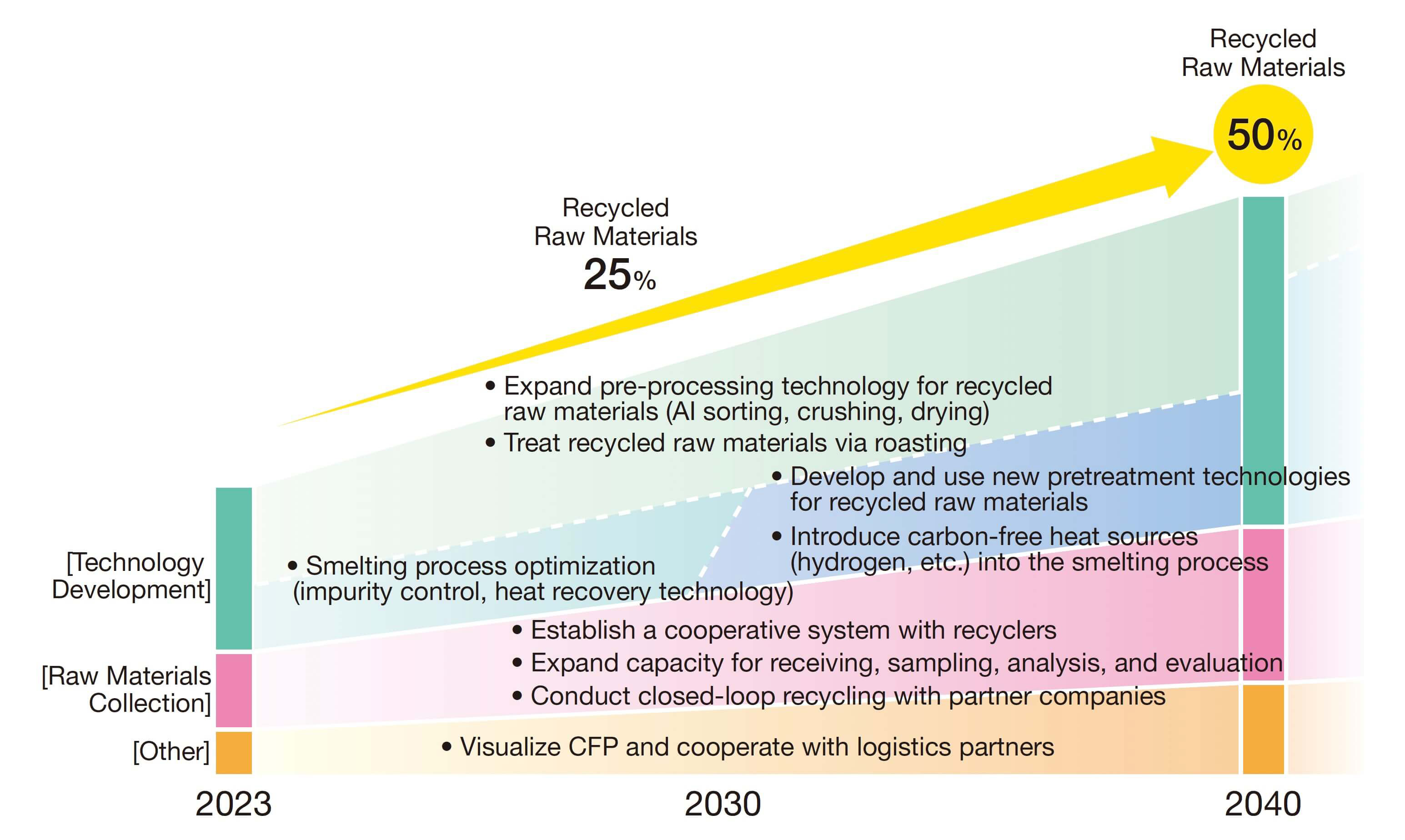
Our flash smelting furnace process not only uses the reaction heat of the raw copper concentrates efficiently to dissolve raw materials, but also uses the excess reaction heat to melt the recycled raw material, eliminating the need for fossil fuels or other resources. We pursue the optimal combination of copper ore and recycled materials through our Green Hybrid Smelting to achieve sustainable production of copper. Here, we aim to evolve Green Hybrid Smelting that uses 50% or more recycled raw materials (input ratio of raw materials or content ratio in products) by 2040. The table on the right shows specific issues and measures.
Promote Responsible Procurement and Other Measures
The Saganoseki Smelter & Refinery and Hitachi Works are engaged in responsible production activities. In December 2022, these facilities were the first in Japan to receive The Copper Mark, a highly credible assurance framework that demonstrates the copper industry's commitment to the green energy transition.
The Copper Mark is a certification program established in 2019 requiring compliance with 32 standards, including standards for the environment, human rights, community, and governance. Both of the business sites will continue to undergo evaluations based on the various standards established under The Copper Mark.
In October 2023, the Caserones Copper Mine (Chile), in which we hold a partial interest, obtained The Copper Mark. With this certification, all concession-holding copper mines and copper smelting and electrorefining plants are now certified. As international demands for ESG initiatives increase, we will continue efforts to strengthen the competitiveness of sustainable businesses.
Form Green Enabling Partnerships
Green Enabling Partnerships Concept
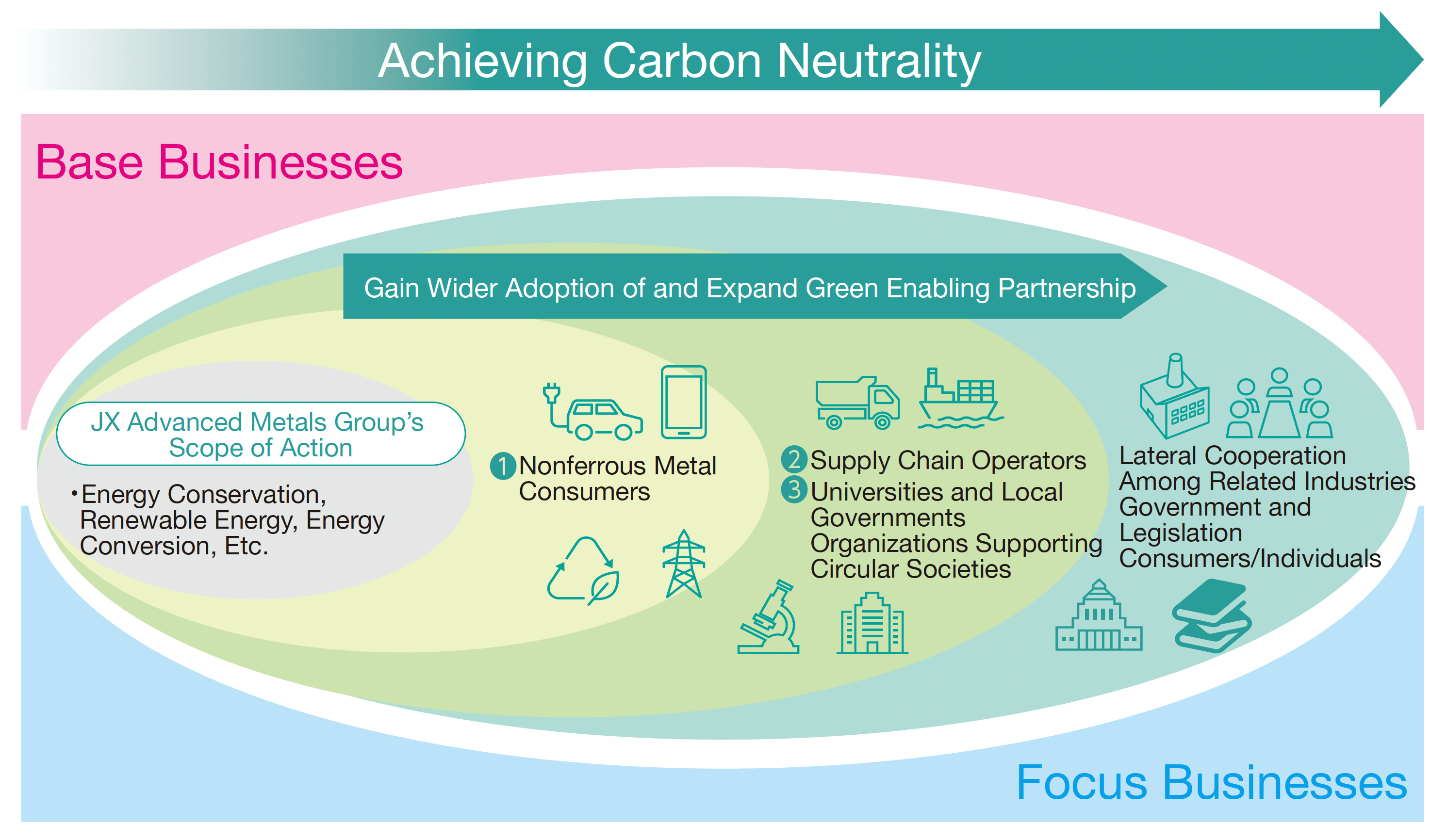
We form Green Enabling Partnerships (GEP) with companies who work together to promote sustainable copper. Through these partnerships, we accelerate the transition to decarbonized, circular economies as well as engage in product and scrap collection, raw materials reuse, and joint technology development. Through GEP, we engage in communication with diverse stakeholders and gather feedback on their needs, resulting in the initiatives outlined on the next page.
Our Efforts to Promote Recycling
Co-Creation of Resource Recycling With Customers
In order to promote resource recycling, it is essential that we not only promote our own initiatives as an individual company, but also to cooperate with our customers, including manufacturers of products that use copper, and consumers of final products. By proposing new recycling schemes that are attractive and reliable for users, we can achieve a balance between corporate activities and resource recycling. To that end, we proposed a new copper supply scheme with the aim of co-creating resource recycling with our customers.
Our Proposed New Recycling Scheme
In January 2024, we announced the launch of two types of 100% recycled electrical copper using the mass balance method: The Partnered Closed Loop 100% mass balance method (PCL100/mb) and the Mixed Recycle 100% mass balance method (MR100/mb),” which will be launched during the fiscal 2024.
One of the new schemes, the PCL100/mb, involves using recycled materials from customers (Company A in the diagram) that have collected used products or generated process scrap in their factories. The product is returned to customers as 100% recycled electrolytic copper with a guaranteed origin (which means to ensure the copper is sourced from Company A).
In the actual copper smelting process, recycled raw materials from Company A are mixed with other recycled raw materials and copper concentrate for smelting treatment. This makes it impossible to extract only copper originating from recycled raw materials from Company A.
However, by using the mass balance method, it is possible to link the electrolytic copper to the recycled material. We accurately analyze the volume of copper contained in the recycled materials from Company A and will strictly manage the electrolytic copper produced to ensure it does not exceed that amount, thereby designating it as copper sourced from Company A. In July 2024, the validation of this management system (CoC management system) was completed by a third party. On the other hand, in the case of MR100/mb, the origin of the raw material is not separately linked to the electrolytic copper.
The management of the recycled materials collected from the market and their copper content will enable us to supply 100% recycled electrolytic copper using the mass balance method.
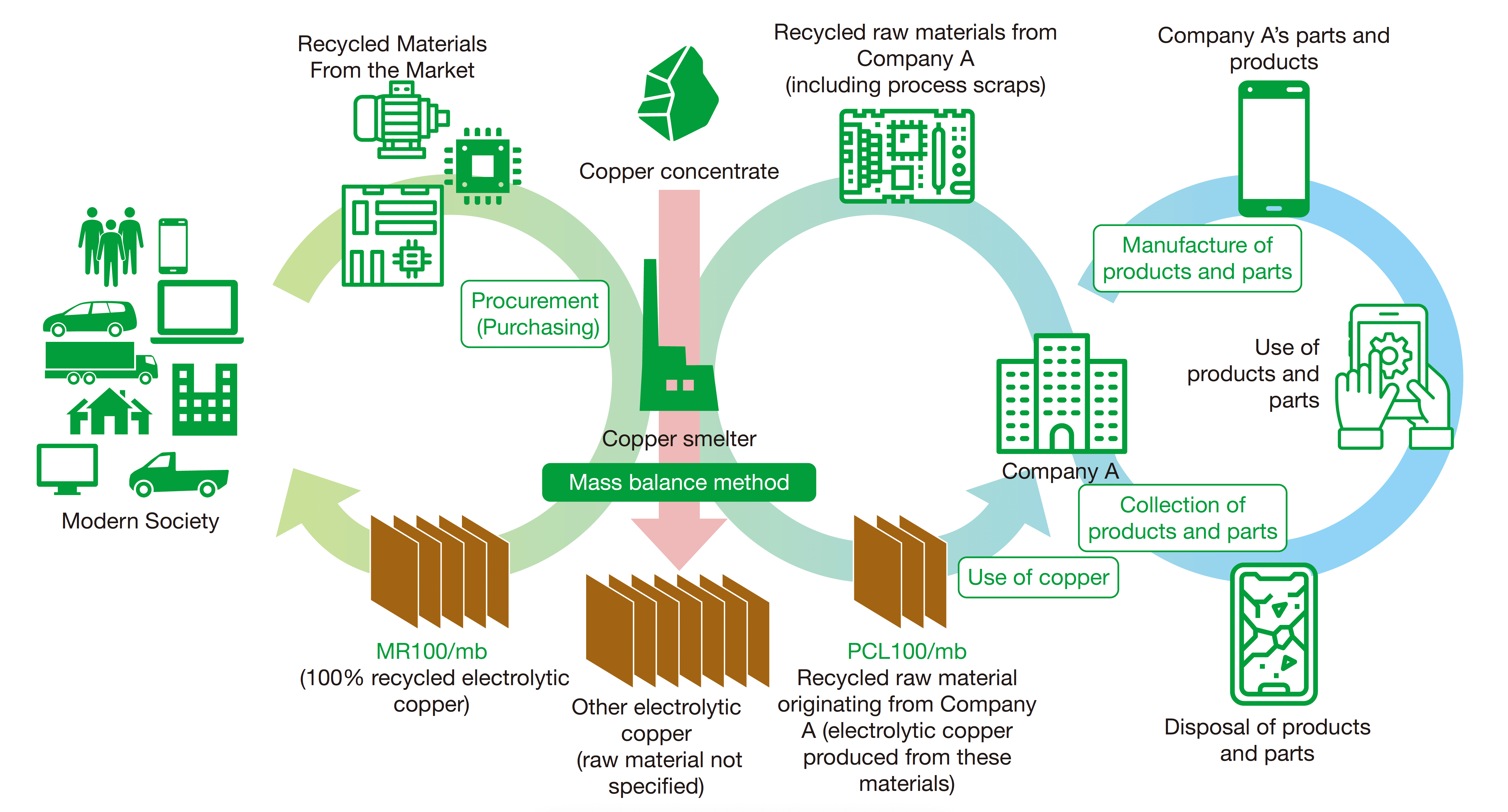
Carbon Footprint (CFP) of Recycled Electrolytic Copper
Electrolytic Copper CFP and its Breakdown
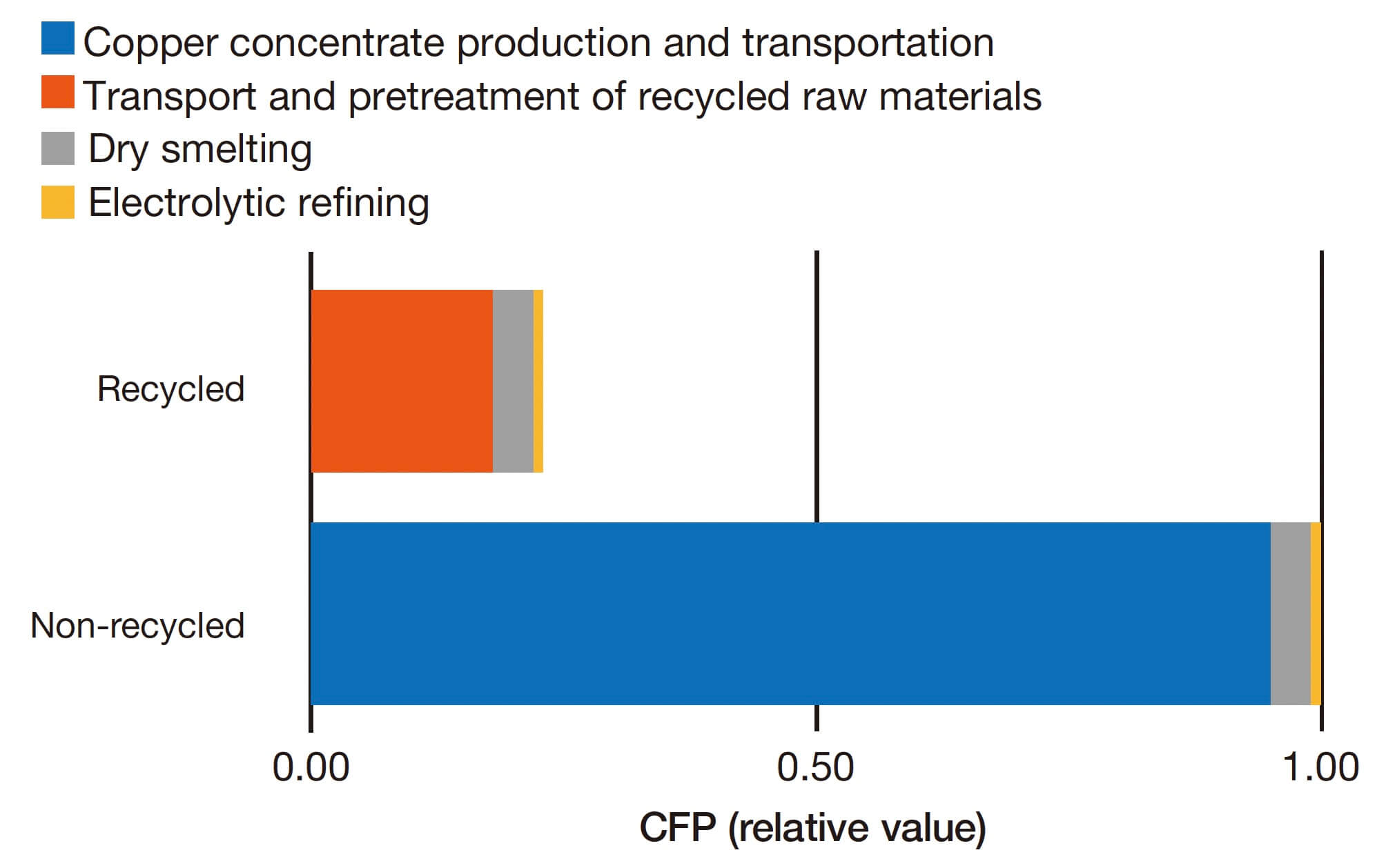
In 2023, we obtained third-party certification for the calculation of CFP values, and we are actively engaged in calculating the CFP for various product categories. Our CFP calculation shows that the CFP of recycled electrolytic copper is approximately 25% that of non-recycled products. This is primarily because the CFP resulting from raw materials are very different. With this in mind, the Company has determined that it is essential to further increase the recycling rate and reduce emissions associated with the procurement of copper concentrates from copper ore and their transportation. We are prioritizing efforts in green hybrid smelting, collaboration with mining companies through the Green Enabling Partnership, and reducing emissions from the transportation of copper concentrates.
Spiral Model With Customers
The combination of increasing recycling ratios and utilizing mass balance methods can produce a variety of benefits. PCL100/mb, for example, contributes to our ability to secure a stable supply of recycled raw materials with the cooperation of our customers. There are benefits for customer (copper consumers) as well, such as the potential to obtain recycled electrolytic copper at quality and cost levels similar to traditional materials, improved raw material traceability, and a reduction in the CFP of procurement materials. Moreover, focusing on the collection of waste products and process scrap produced by customers, which serve as the raw materials for PCL100/mb, not only facilitates the procurement of recycled electrolytic copper but also has the potential to contribute to the promotion of resource recycling throughout society. In this way, our proposed model for supplying 100% recycled electrolytic copper provides various benefits through interaction between our customers and us, fostering a win-win relationship. We have launched activities aimed at social implementation of this product (PCL100/mb) as the Cu again project, and discussions are underway with stakeholders from various industries.
Spiral Model With Partner Companies
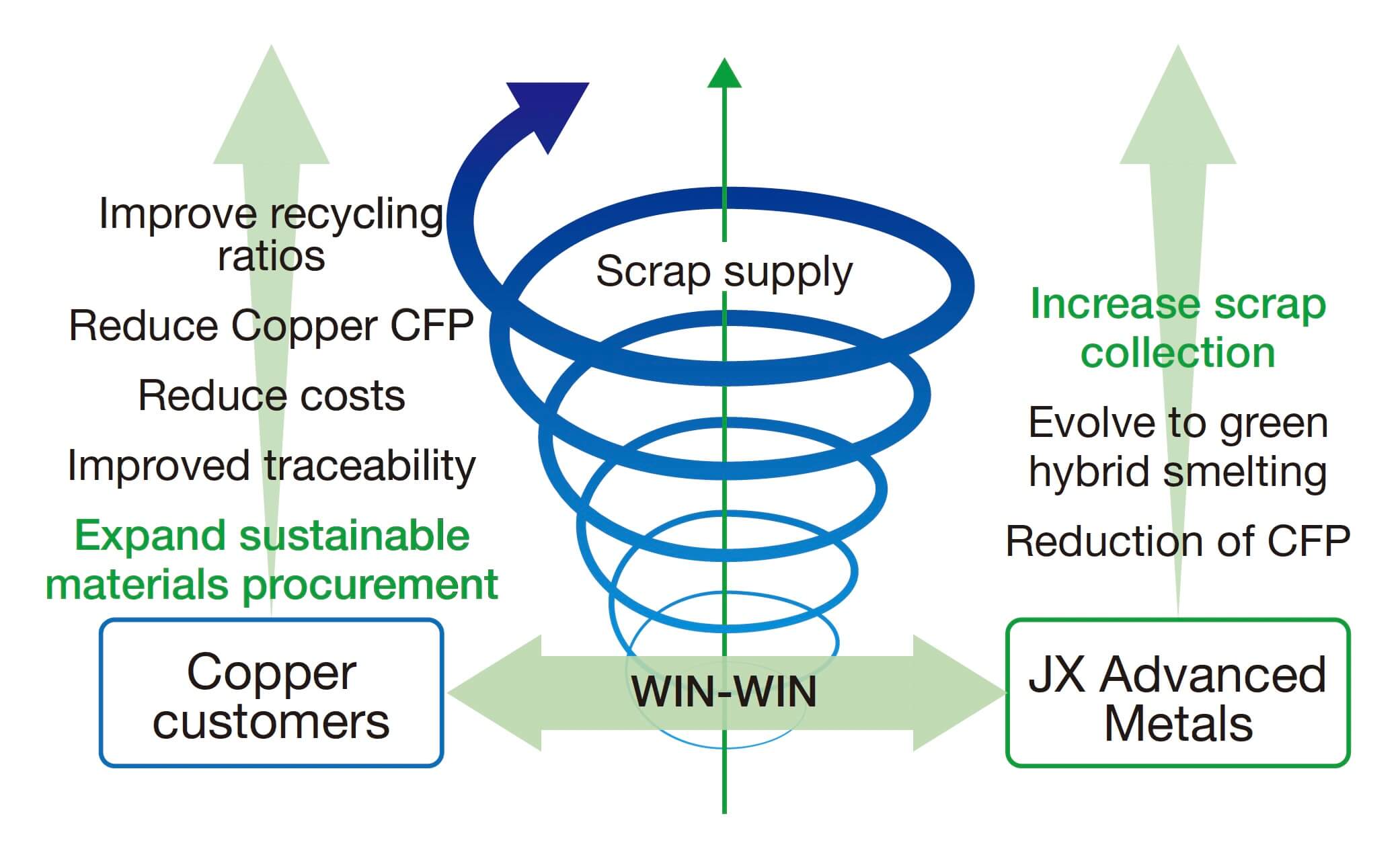
Cu again design
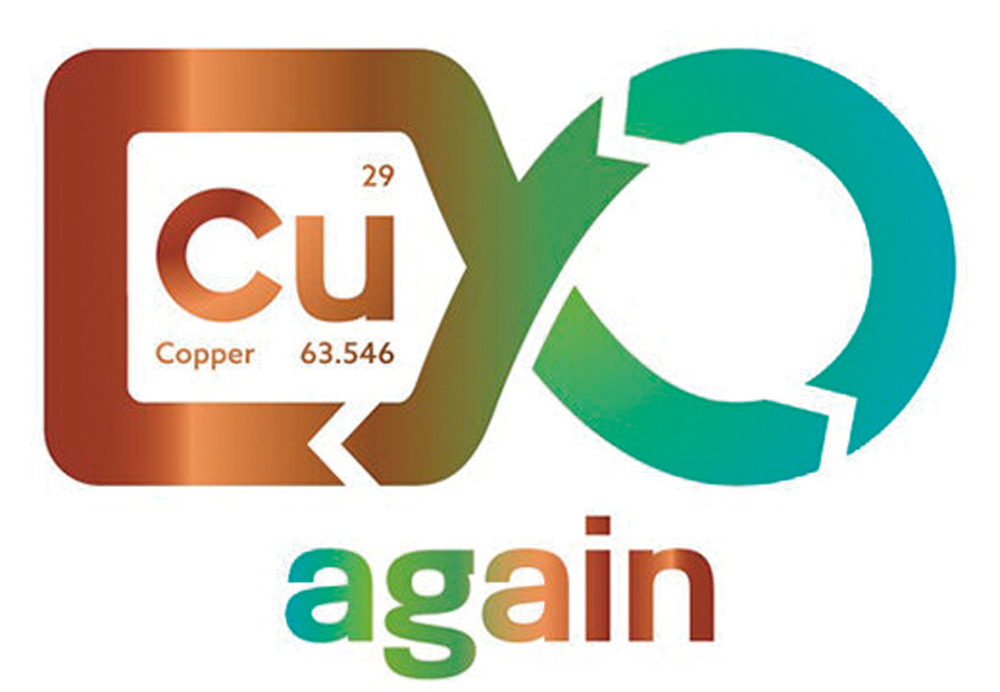
Initiatives to Increase Collection of Recycled Raw Materials (Cyclic Sectors)
We are advancing the establishment of systems for increased collection and processing of recycled raw materials as we aim to achieve the Sustainable Copper Vision. To strengthen our collection system for recycled raw materials, we acquired shares in eCycle Solutions Inc., a Canadian recycler, in August 2022. In April 2024, in collaboration with Mitsubishi Corporation, we established JX Metals Circular Solutions Co., Ltd. to promote the reuse of waste electrical appliances, discarded electronic devices, and end-of-life automotive lithium-ion batteries, officially commencing operations in July of the same year. By leveraging Mitsubishi Corporation’s cross-industry global network and expertise, we aim to expand the collection of recycled raw materials and enhance collaboration across the entire supply chain, with the goal of increasing the recycling of non-ferrous metal resources such as copper and minor metals.
Mass Balance Method Concept
The mass balance method is used when raw materials with differing properties and origins are mixed during the manufacturing process, resulting in products that cannot be distinguished based on their raw materials. This approach allocates specific properties to a portion of the product based on the input ratio of raw materials with those properties.
Example of Mass Balance
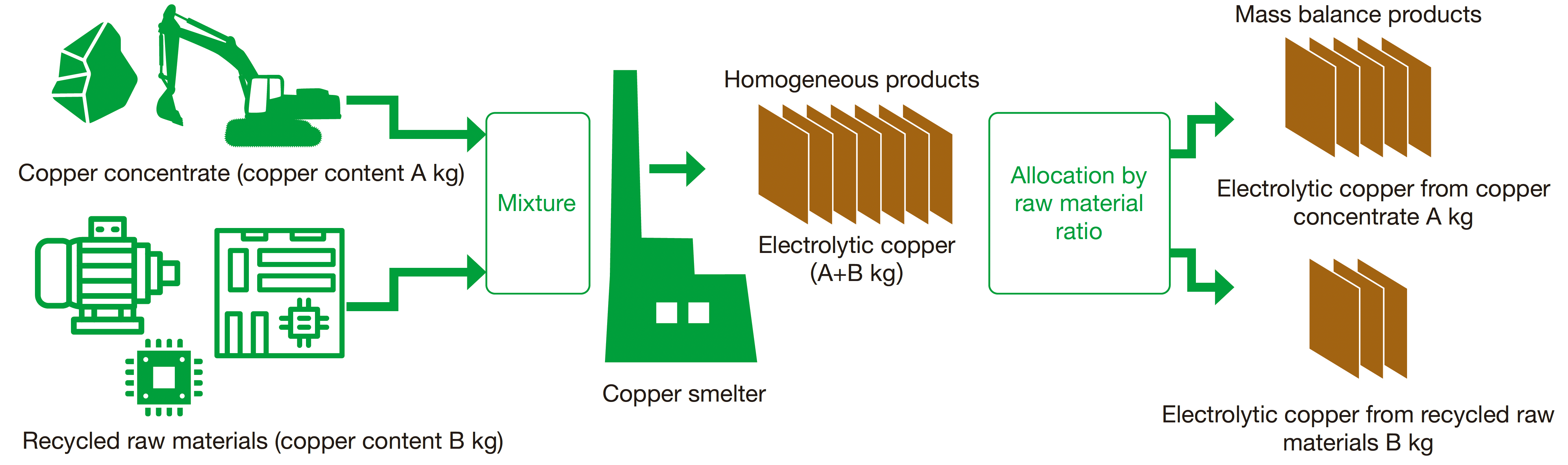
Other Initiatives for Environmental Conservation
Closed-Loop Recycling of Automotive Lithium-Ion Batteries (LiB)
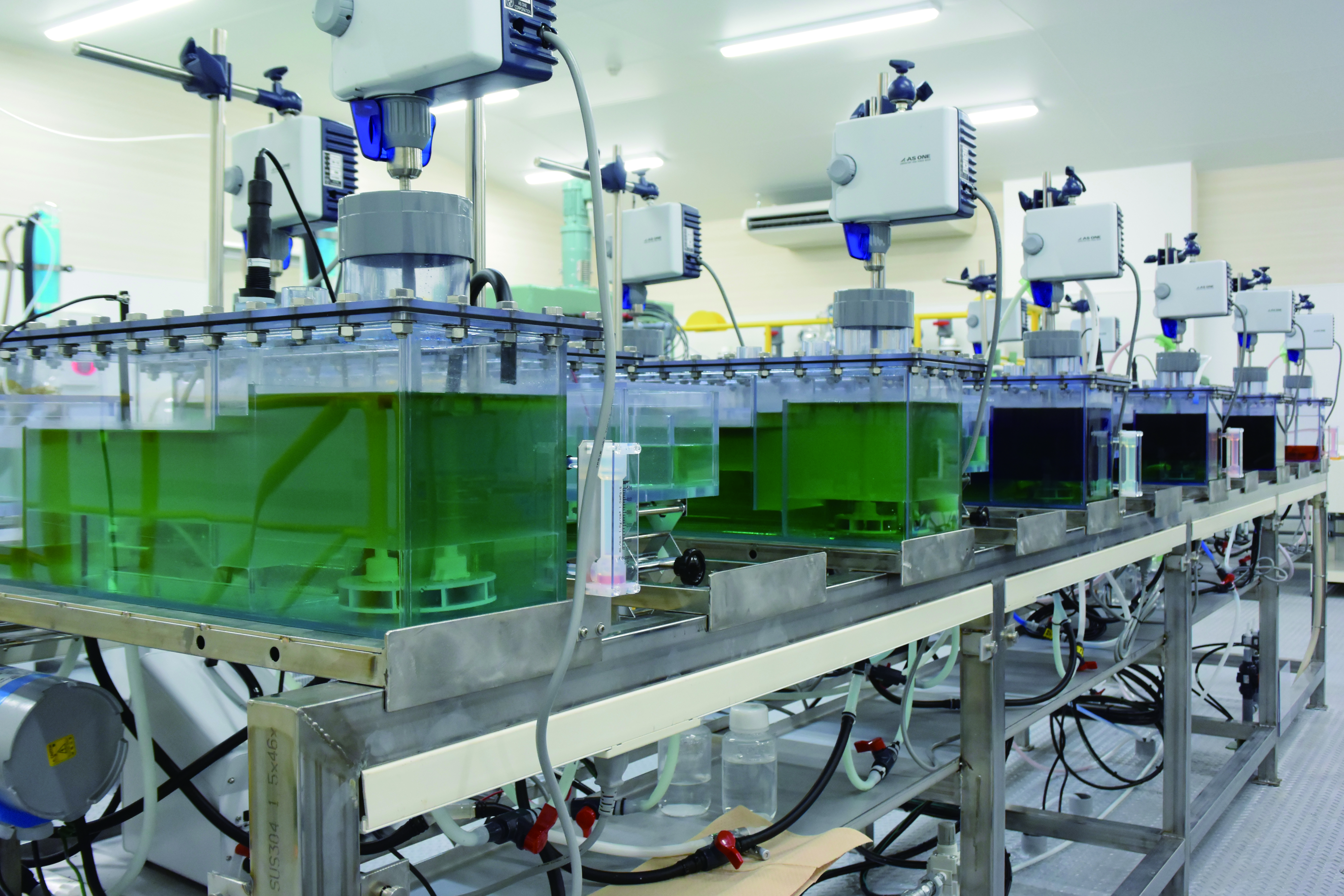
Minor metals such as nickel, cobalt, and lithium used in LiB are not produced in Japan, but are rather concentrated in a specific set of countries and regions. Reducing the environmental impact and supply chain risk associated with the use and securing of these mineral resources has become a serious social issue.
In 2020, we established a closed-loop recycling process to recover minor metals from end-of-life automotive LiBs, reusing these metals as raw materials for automotive LiBs in continuous processing bench-scale test equipment installed at Hitachi Works.
Scaled-up versions of this process are being gradually introduced at JX Metals Circular Solutions Tsuruga Co., Ltd. In addition to the inauguration of a high-purity nickel sulfate recovery facility in 2021 and a high-purity cobalt sulfate recovery facility in 2022, we have started operations for a high-purity lithium carbonate recovery facility in April 2023, and are demonstrating our recycling process there. Going forward, we will provide high-purity recycled metal salts to our business partners and demonstrate closed-loop recycling for automotive LiB through the supply chain.
In 2022, our project for the Development of Technology for Closed-Loop Recycling for Automotive LiB was selected for funding by the Green Innovation Fund of the New Energy and Industrial Technology Development Organization (NEDO). Utilizing this fund, we will further advance recycling technology toward the social implementation of closed loop recycling for automotive LiB in collaboration with universities and public research institutions. Through this initiative, we aim to strengthen the LiB supply chain and contribute to the establishment of a circular economy.
Inauguration of R&D Facility for Automotive Lithium-Ion Battery Recycling (Germany)
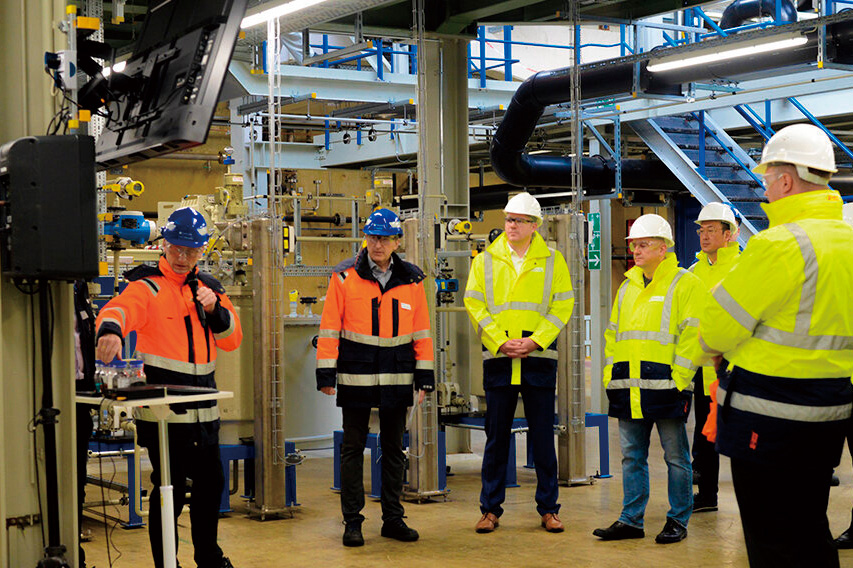
JX Metals Circular Solutions Europe GmbH, a member of the JX Advanced Metals Group, has established an R&D facility for automotive LiB recycling at the TANIOBIS GmbH location in Goslar. The facility is based on hydrometallurgical processes developed by the Group and by using this facility we will demonstrate closed-loop recycling for automotive LiB under the HVBat-Cycle consortium. This consortium includes German companies, such as the Volkswagen Group, research institutions, and academic institutions, and receives support from the German Federal Ministry for Economic Affairs and Climate Action (BMWK). At this facility, we will focus on optimizing processes to recover high-purity battery materials with high yield from black mass (battery power) provided by the Volkswagen Group.
Acquisition of Certification for Recycling and Reuse Operators Under the Basel Convention
The JX Metals Smelting Co. Ltd., Saganoseki Smelter & Refinery received certification as a recycling and reuse operator under the Law for the Control of Export, Import, and Others of Specificized Hazardous Wastes and Other Wastes (Basel Convention) on August 23, 2023.
The so-called Basel Law establishes rules to ensure the precise and smooth implementation of the Basel Convention, the international framework for regulating the transboundary movement and disposal of waste. Recycling and reuse operators are business operators that are able to recycle and reuse waste appropriately and in a manner that preserves the environment. The recent certification indicates that the efforts in the Metals & Recycling Business at the Saganoseki Smelter & Refinery have been evaluated as meeting the requirements for certification.
Co-Hosted Workshop on Proper Disposal and Resource Recovery of E-Waste (Vietnam)
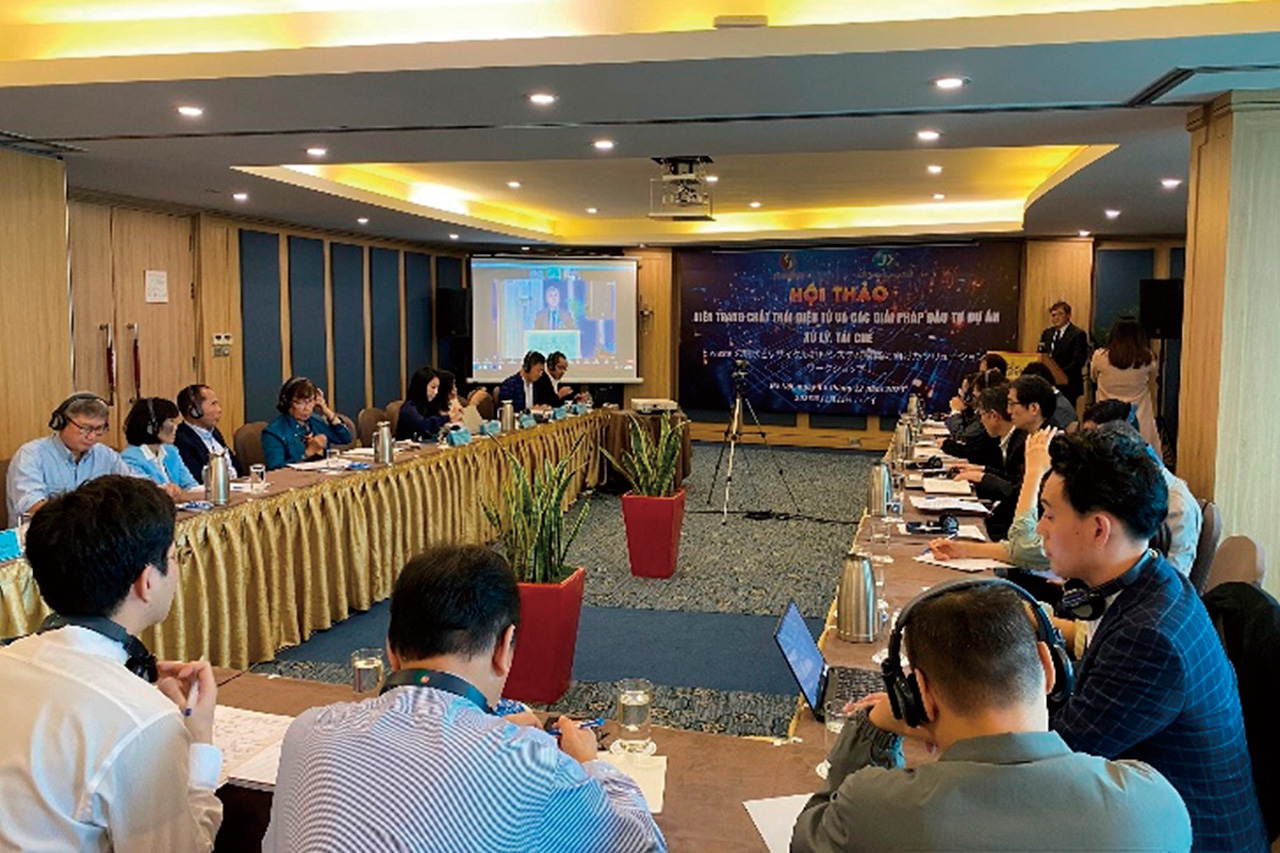
On December 15, 2023, we co-hosted a workshop titled Current Status of E-waste and Solutions for Building Recycling and Processing Systems with the Media Center of the Ministry of Natural Resources and Environment (MONRE) in Vietnam. The workshop was conducted as part of the Appropriate Treatment of E-waste in Hanoi or Ho Chi Minh City and Examination of Metal Resource Recovery in Japan project. This project was approved by the Ministry of the Environment of Japan under its initiative to promote the overseas development of Japan's circular economy industries. On the day of the workshop, representatives from key stakeholders in Vietnam's industry, education, and government sectors participated, including the MONRE, Hanoi University of Science and Technology, the Vietnam Waste Recycling Association, and the Vietnam Electronic Industries Association. Additionally, Japan's Ministry of the Environment participated online.
During the workshop, the Company shared the expertise we have gained from years of operating in the smelting and recycling industry. We highlighted the potential for reducing environmental impacts through technical support and discussed our contributions to achieving metal resources recycling. From the Vietnam-ese side, there were presentations on the country's environmen-tal protection laws, rules regarding E-waste collection and treatment, and the current status and future prospects of E-waste generation and processing. The presentations led to lively discussions in the second half of the workshop, focusing on the challenges and considerations for commercializing E-waste recycling in Vietnam.
Initiatives for Zero Emissions
Our Smelting, Refining, and Recycling Business generally buries secondary waste (incinerated ash, incineration residue, etc.) generated during the treatment of industrial waste as the final method of disposal. Pursuing the notion of never discard, never bury, the JX Advanced Metals Group strives for zero emissions by combining our environmental and recycling businesses to build and operate a system to recycle these secondary wastes and the valuable metals contained therein. Affiliated companies involved in our Environmental Business work with the Metals and Recycling Business sites to achieve a recycling-oriented society.
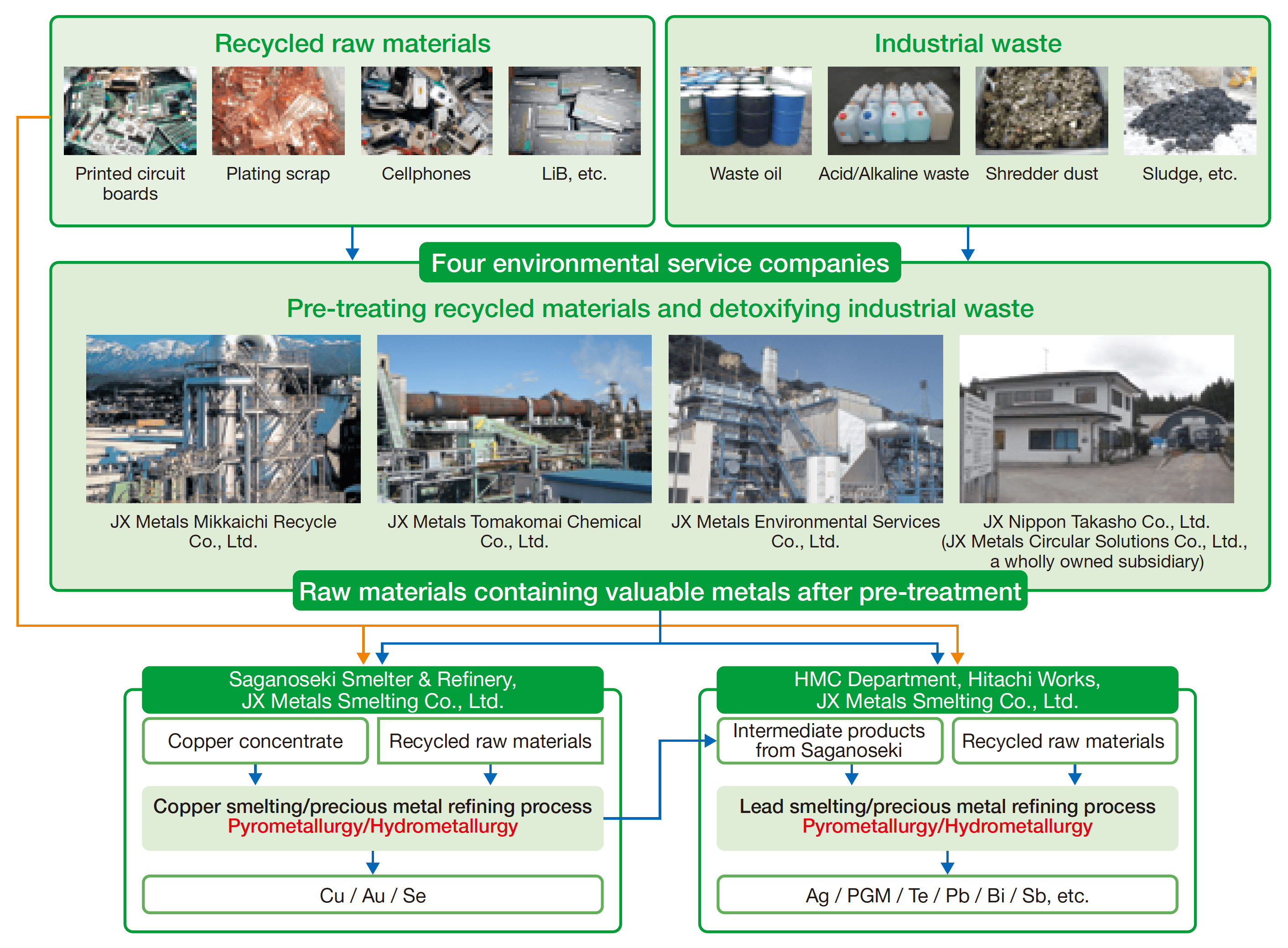