
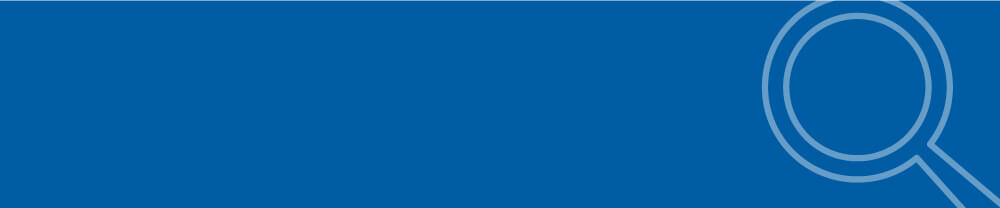
Quality Control in the Supply Chain
The Group recognizes that our social mission is to provide a stable supply of nonferrous metals and materials in order to contribute to the sustainable development of society. Based on this policy, we aim to improve the level of quality control throughout the entire supply chain.
JX Advanced Metals Group Basic Quality Policy
The JX Advanced Metals Group hereby sets forth, and acts in observance of, this Basic Quality Policy in order to contribute to the development of a sustainable society while recognizing that its social mission is to stably supply nonferrous metals and materials.
- 1.Grasp the requirements of customers and society correctly in order to offer products and services that customers can trust and that satisfy their needs.
- 2.Improve and maintain quality in all processes from development, design, and production to delivery, while paying due attention to safety and environmental conservation.
- 3.Establish a quality management system, carry out continual improvements, and develop human resources.
- 4.Comply with all pertinent laws and regulations of Japan and other countries, and provide customers and society with accurate in-formation on quality.
Establishing and Operating a Quality Management System
The Group has and operates a quality management system (QMS) to realize our Basic Quality Policy. We work to continually make quality improvements through steady PDCA cycles, aiming to realize better quality through the QMS. As one measure, Company sites both in Japan and overseas have acquired QMS third-party certification (ISO 9001, etc.).
In addition, the Group reviews quality improvement activities and establishes action plans through the Quality Management Meeting, which is made up of top management. We also hold Quality Meetings twice annually to share information on quality management. Participants share the action plans adopted at Quality Meetings and share issues encountered and good prac-tices found at each manufacturing site, fostering interactions among managers. Furthermore, we are working to improve the effectiveness of internal quality audits, automate inspections, and strengthen the training of quality control personnel.
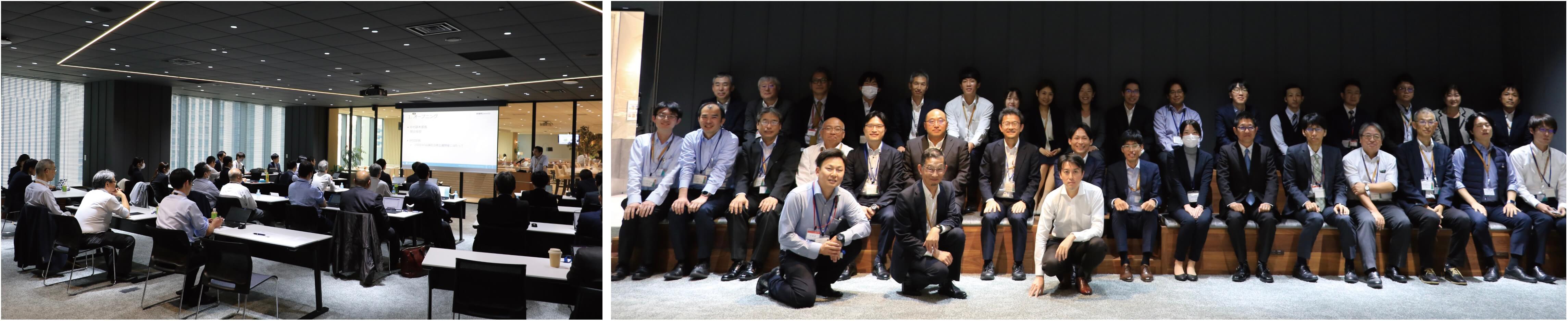
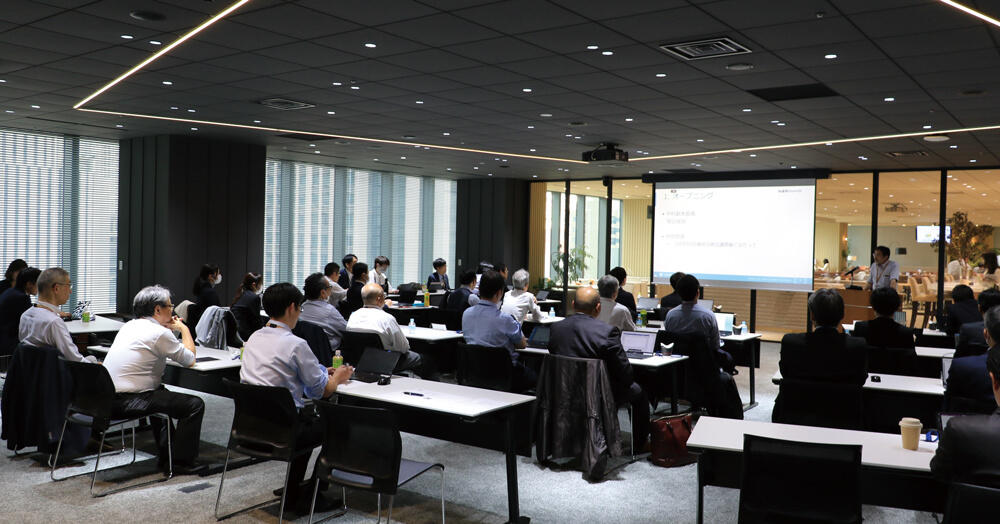
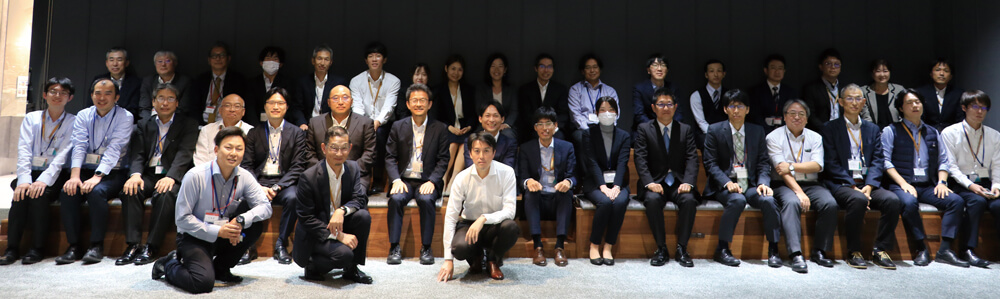
Main Manufacturing Sites With Third-Party QMS Certifications
[Domestic]
- Isohara Works, Kurami Works, Hitachi Works (Copper Foil Department)
- Ichinoseki Foil Manufacturing Co., Ltd.
- Kitaibaraki Precision Co., Ltd.
- JX Advanced Metals Coil Center Co., Ltd. (Kurami Office, Tatebayashi Office)
- JX Metals Trading Co., Ltd. (Takatsuki Plant)
- JX Metals Smelting Co., Ltd. (Saganoseki Smelter & Refinery, Hitachi Works)
- JX Metals Resources Exploration & Development Co., Ltd.
- TANIOBIS Japan Co., Ltd. (Head Office, Mito Plant)
- Tokyo Denkai Co., Ltd.
- Toho Titanium Co., Ltd. (Head Office/Chigasaki Plant, Hitachi Plant, Yahata Plant, Wakamatsu Plant, Kurobe Plant)
- Japan Copper Casting Co., Ltd. (Saganoseki Plant)
- Furuuchi Chemical Corporation
[Overseas]
- Nippon Mining & Metals (Suzhou) Co., Ltd.
- JX Nippon Mining & Metals Dongguan Co., Ltd.
- Nikko Metals Taiwan Co., Ltd. (Longtan Works, Kuanyin Works)
- JX Metals Philippines, Inc.
- JX Metals USA, Inc.
- JX Metals Korea Co., Ltd.
- TANIOBIS GmbH (Goslar)
- TANIOBIS Smelting GmbH & Co. KG (Laufenburg)
- TANIOBIS Co. Ltd. (Map Ta Phut)
- Materials Service Complex Malaysia Sdn. Bhd.
- Materials Service Complex Coil Center (Thailand) Co., Ltd.
Quality Control Department Activities
The Quality Control Department is in charge of planning, proposal, promotion, and oversight for enhancement of Group-wide quality control. This department is also engaged in clarifying Group-wide QMS requirements, improving the effectiveness of internal quality audits, supporting quality improvement activities and quality control training at manufacturing sites, introducing DX to quality management tasks.
In fiscal 2023, the Quality Control Department conducted internal quality audits at 24 domestic and overseas sites. In addition, to improve the auditing skills of Quality Control Department staff, four new employees took the JRCA*1 and IRCA*2-certified ISO 9000 auditor training course and passed the qualification examination in fiscal 2023. The Quality Control Department currently has 11 employees who have passed the training course for ISO 9001 certified auditors and are actively engaged in quality audits.
- *1JRCA stands for Japanese Registration of Certified Auditors
- *2IRCA stands for International Register of Certificated Auditors
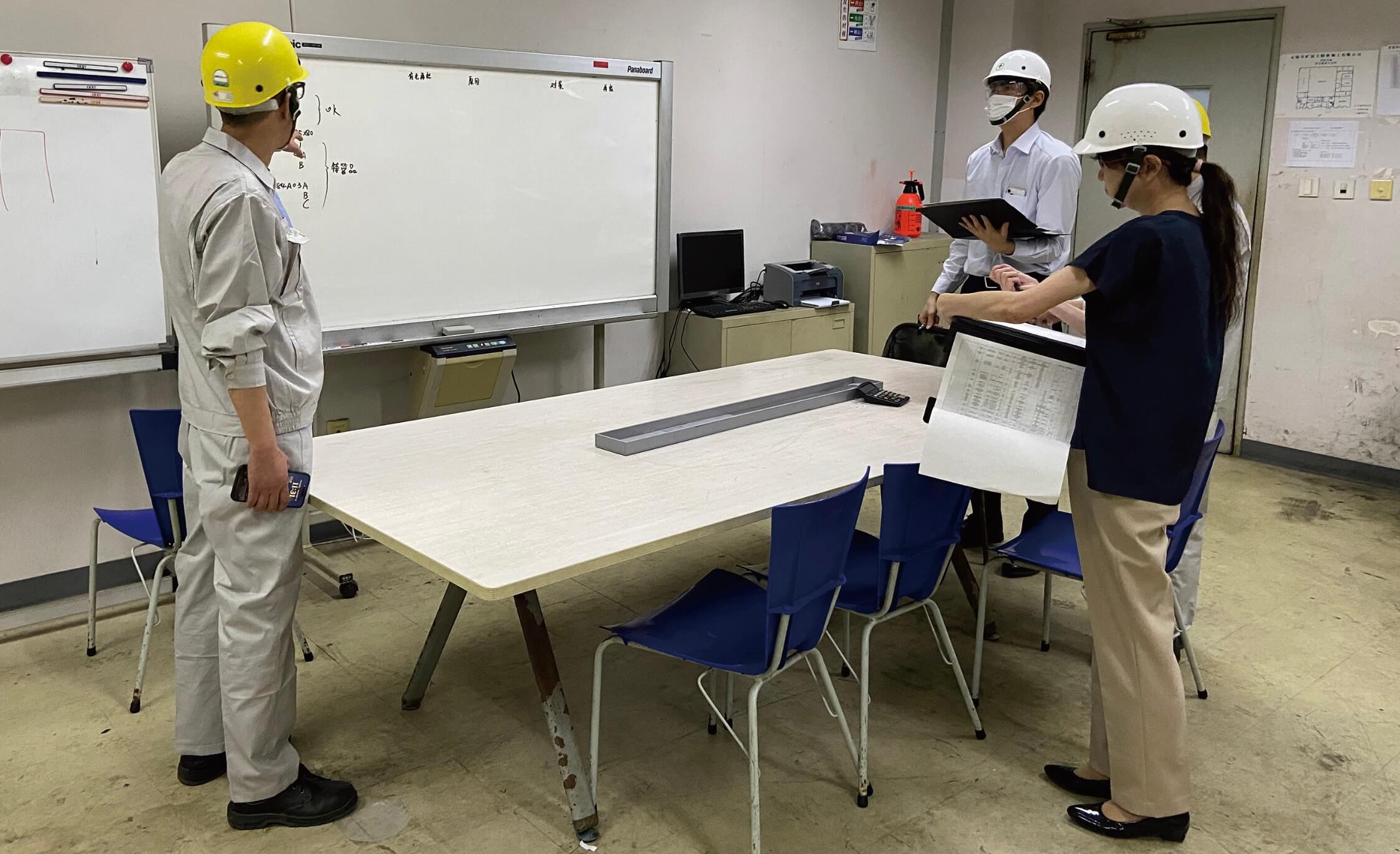
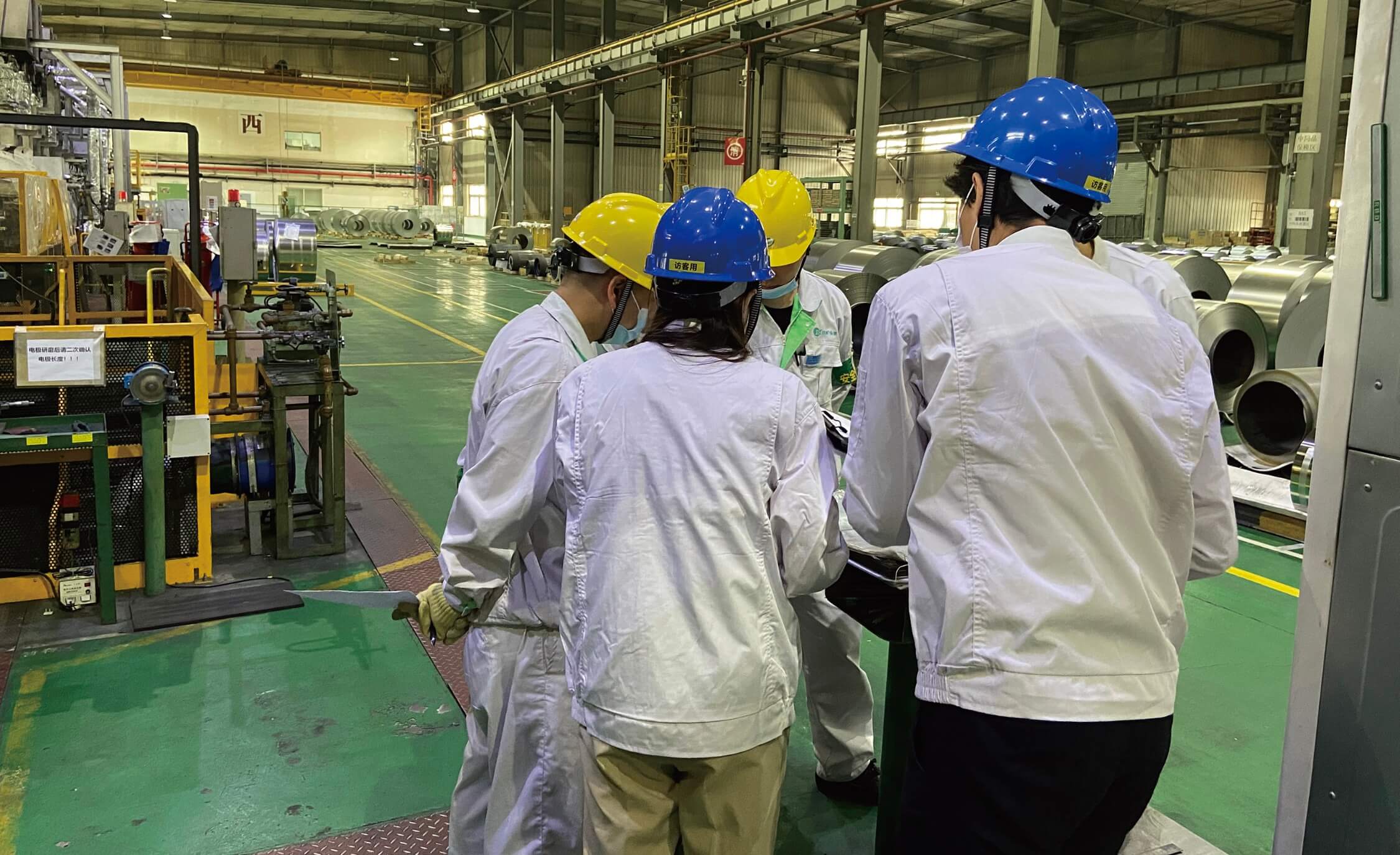
Voice From the Quality Control Department
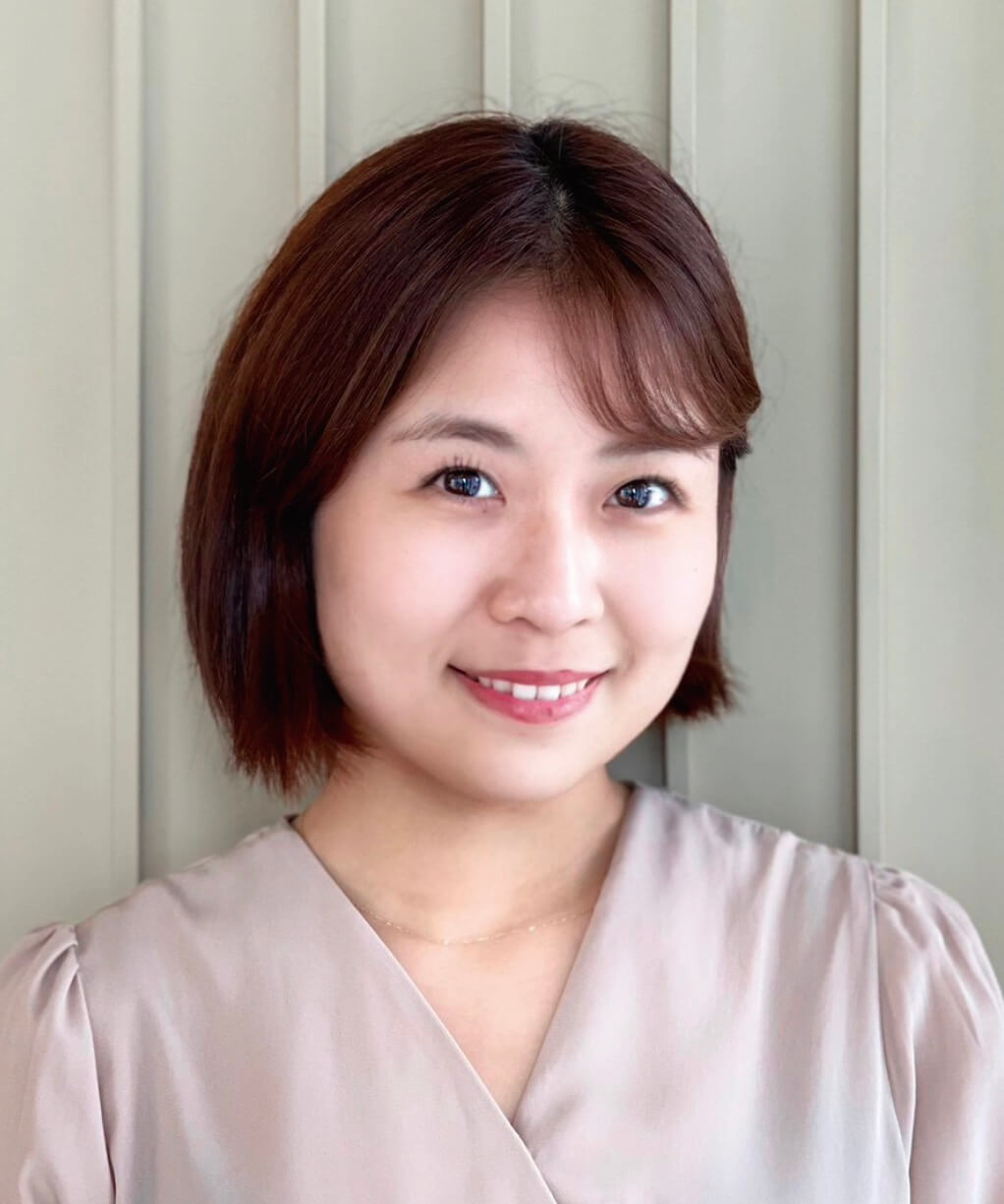
Quality Control Department
Hoso Marie
One of the important tasks handled by the Quality Control Department is internal quality audits. I had no previous experience in the field, and it was a completely different from my major as a student. However, I believed that being able to conduct evaluations from a different perspective would contribute to our quality improvement efforts. With an eye towards becoming an internal quality auditor, I was able to pass the JRCA/IRCA ISO 9000 auditor certification examination with the support of study groups within our Company and outside seminars. I would like to thank everyone in the department who helped me obtain the certification. Moving forward, I want to use this as a source of confidence and contribute to maintaining and improving the quality that will satisfy our customers.
Liability Claims
In fiscal 2023, no claims were pursued under the Product Liability Act due to personal or property damage caused by defects in products made by the Group.
Providing Information on Products and Services
In accordance with the Basic Quality Policy, the Group provides customers with information on its products and services through product specifications and Safety Data Sheets (SDS)*. For example, sulfuric acid sold by Group companies is designated as a deleterious substance under Japan's Poisonous and Deleterious Substances Control Act. By limiting our business partners to sellers of poisonous or deleterious substances and issuing SDSs, we strive to prevent serious negative effects on the occupational health and safety for our customers and their employees after delivery.
- *Safety Data Sheet (SDS): A document containing information on the hazards and toxicity of chemicals to ensure safe handling
Quality Assurance Initiatives With Suppliers
Cooperation with suppliers is essential for thorough quality as-surance. Our efforts include conducting regular evaluations and quality audits for JX Advanced Metals Group suppliers based on quality control criteria and requirements, reducing quality risks, and improving the quality level of our suppliers. We also conduct Supplier Surveys to promote mutual understanding with our suppliers.
Promotion of Personnel Quality Education
The Group ensures that all employees are thoroughly familiar with the Basic Quality Policy through quality control training. In addition, we provide quality control training to all employees to improve their problem identification and resolution capability, help them to logically infer the root cause of a problem, independently resolve problems, and improve the quality of their work. These training programs range from introductory to advanced courses according to the level of the participants and reflect carefully planned courses according to job rank and years of employment, and have become an established part of em-ployee training.
Starting in fiscal 2020, the Company's Quality Control Department began encouraging internal quality auditors to acquire qualifications such as QMS Auditor, and conducting review training performed by outside instructors to improve competence.

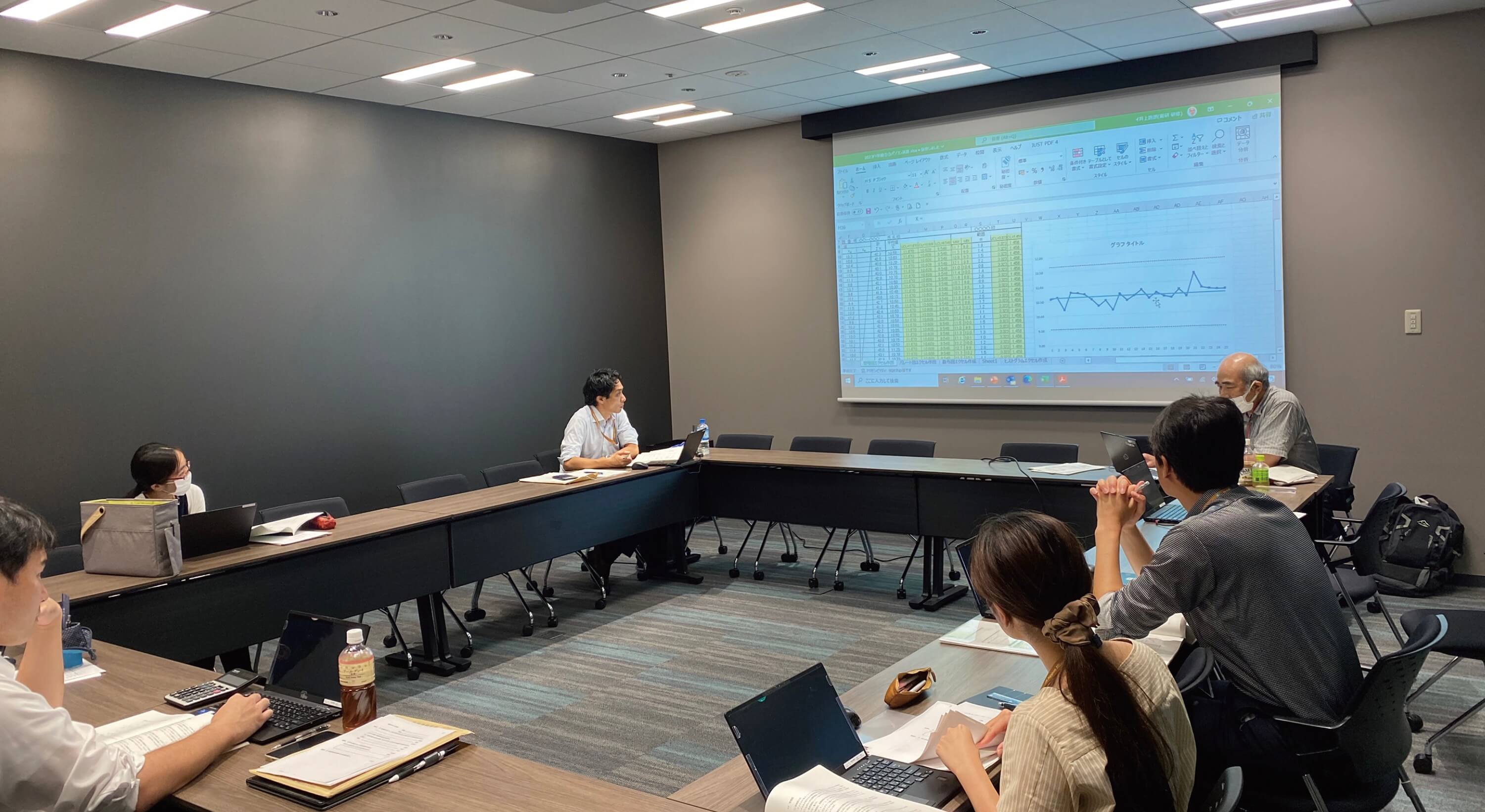