
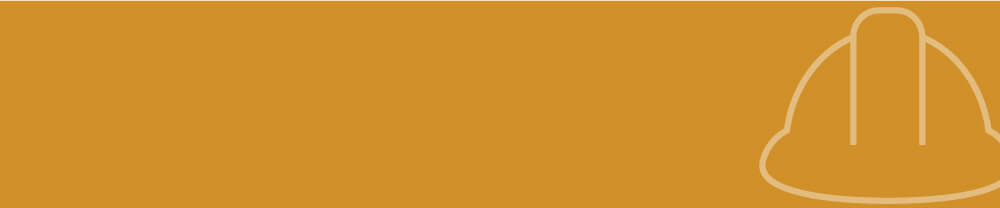
Ensure Safety and Promote Health
Recognizing that the safety and health of our employees is the foundation for sustainable growth, the JX Advanced Metals Group is committed to creating a workplace environment that ensures safety and promotes health.
JX Advanced Metals Group Basic Policy on Health and Safety
We place the highest priority on ensuring the health and safety of people working in all areas of business operations at the JX Advanced Metals Group and create attractive workplaces by providing safe, secure, and healthy working environments.
- 1.We will comply with all laws and regulations relating to health and safety, establish voluntary standards required to achieve compliance, and rigorously manage and adhere to such standards.
- 2.We will strive to continuously improve and enhance industrial health and safety management systems and achieve health and safety goals.
- 3.We will actively provide information and education in order to develop human resources that think and act spontaneously, and raise health and safety awareness throughout the organization.
- 4.We will identify hazards in all areas of business operations, work to eliminate such hazards and reduce risk, steadily achieve annual accident reduction targets, and ultimately aim to ensure no accidents ever occur.
- 5.We will work to maintain and improve employees’ mental and physical health by ensuring good communication and comfortable working environments and taking steps to maintain health and prevent sickness.
Organization for Occupational Health and Safety Management
The Group maintains health and safety committees and other bodies at operating sites and Group companies in keeping with the Industrial Safety and Health Act. We have also established a system to have discussions with workers, including those from subcontractors stationed permanently, within the framework of our health and safety management system. At our head office, the Central Health and Safety Committee meets once a year, attended by representatives (key safety managers and labor union branch committee chairs) from the divisions and operating sites. The Central Health and Safety Standing Committee meets five times a year, attended by standing committee members of the former (safety managers at each division and the three officers from the Central Labor Union). We also hold joint labor/management health and safety visitations (once a year) and Group safety supervisors’ meetings (twice a year) to exchange information on health and safety. In fiscal 2023, we held a hybrid on-site and online meetings, as well as labor/management health and safety visitations at business sites.
Environment and safety audits are conducted periodically by a team under direct supervision of the president at operating sites directly run by the Company (including Group companies within the sites) and major domestic Group companies. Issues discovered in the audits are reported to the president, and also notified to the respective operating sites. In fiscal 2023, we targeted a total of 17 business sites, including 5 overseas sites. No major issues were identified.
Acquiring ISO 45001 Certification
Although we acquired OHSAS 18001 certification, we have been working to introduce ISO 45001 following the abolition of OHSAS in March 2021. ISO 45001 includes JISQ45001 and JISQ45100. Our domestic operating sites strive to acquire the latter to promote company-wide occupational health and safety activities involving a wider range of sites. As of the end of fiscal 2023, 13 domestic operating sites and 3 overseas companies obtained ISO45001 certification. We now aim to obtain certification at 3 domestic sites new to the Group.
We engage in such efforts to improve the level of health and safety throughout the Group further.
Management Policy on Health and Safety for 2023
The Group formulates the Management Policy on Health and Safety each fiscal year. The goals and key policy measures are set based on analysis of health and safety performance in the previous year. The policy is discussed and approved by the Central Health and Safety Committee and then promulgated across the Group.
[Goals]
● Safety and Disaster Prevention Items
- 1.Accidents with lost work days or worse: Zero
- 2.Targets for managing the number of accidents for the entire Group
- (1)
- (Shared domestic/overseas sites) Accidents without lost work days or worse: Reduction of 50% or more of the previous year's results
- (2)
- Occupational injury rate per 1,000 employees in domestic Group (four or more lost work days): 0.70 or less (five injuries or less)
- 3.Fires and explosions: Zero
● Health and Other Items
- 1.Occupational diseases: Zero
- 2.Rate of lost work days due to ordinary illnesses: Reduction by 10% or more from the average in the previous three years
- 3.Cancer screening rate: 70% or more
- 4.Percentage of employees maintaining an adequate weight (BMI less than 25.0): 70% or more
- 5.1% reduction in smoking rate based on FY2022 results
- 6.Traffic accidents (as perpetrator or victim): Reduction by 10%or more from the average in the previous three years
[Key Measures]
- ・
- Promoting inherent safety (strengthening activities to prevent serious accidents from occurring)
- ・
- Expanding health and safety education
- ・
- Strengthening systems for safer construction execution
- ・
- Maintaining and promoting mental and physical health
- ・
- Continuing to implement traffic accident prevention (including work-related traffic accidents)
Safety Education at a Safety Education Center
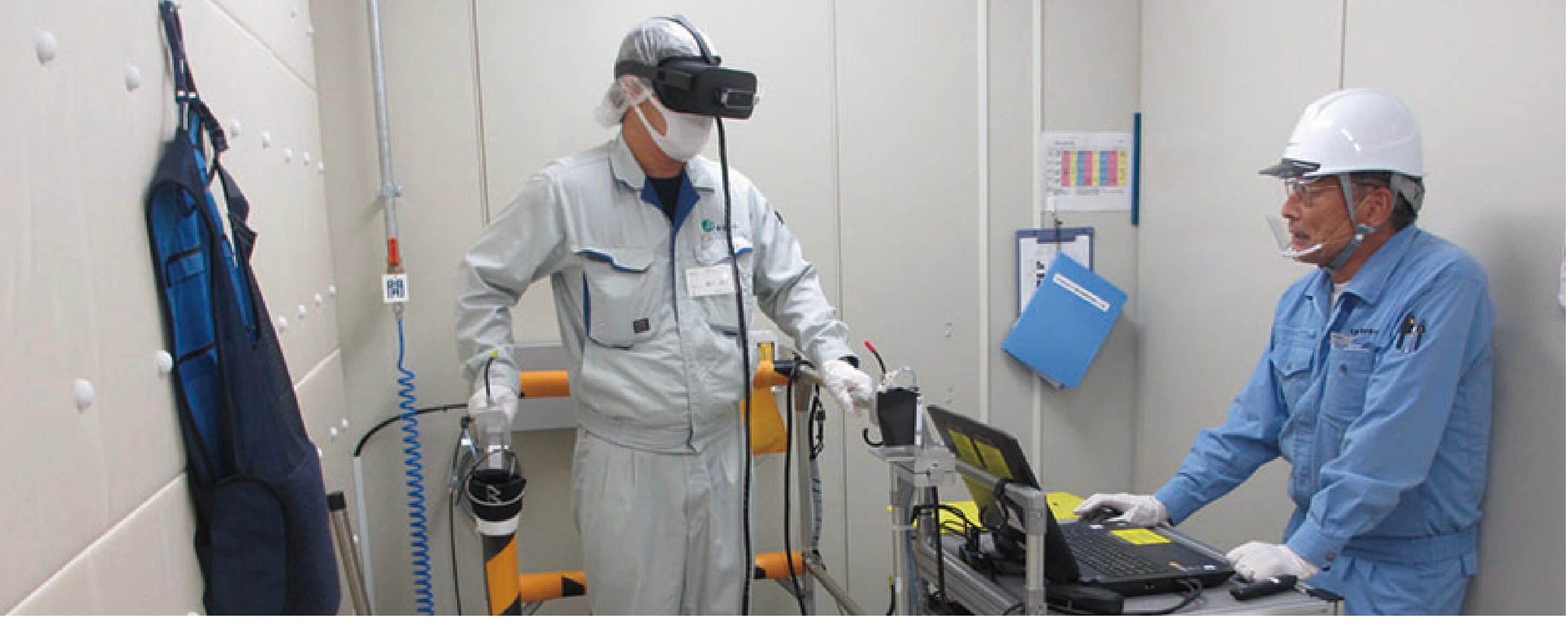
In order to raise the sensitivity to hazard for each and every employee and enhance their safety awareness, the Group has established the Safety Education Center, where we conduct experience-oriented safety education, in Hitachi City, Ibaraki Prefecture. Here, sensitivity to hazards refers to sensing danger correctly. Sharpening this sensitivity leads to workers being able to avoid danger.
Since many of the occupational accidents that have occurred are recurrences of past cases (similar accidents), the center has prepared a program to help workers see that potential accidents are always present, and to improve worker understandings of danger and their sensitivity to hazards through simulated experiences of past occupational accidents. In addition, we have implemented a new educational curriculum that utilizes VR technology, enabling students to have hands-on experience as a victim of an accident or disaster, a situation not easily simulated in real life. In recent years, while the number of occupational accidents among employees has been decreasing, the number of occupational accidents among employees from Subcontractors has become an issue. To address this, we have introduced locational education facilities at our core operating sites to address workplace-specific occupational accidents and improve employee sensitivity to hazards and safety awareness of not only our Group employees but also those of our Subcontractors. The Safety Education Center and the locational education facilities work in unison to eradicate occupational accidents among employees.
Project to establish a health management system
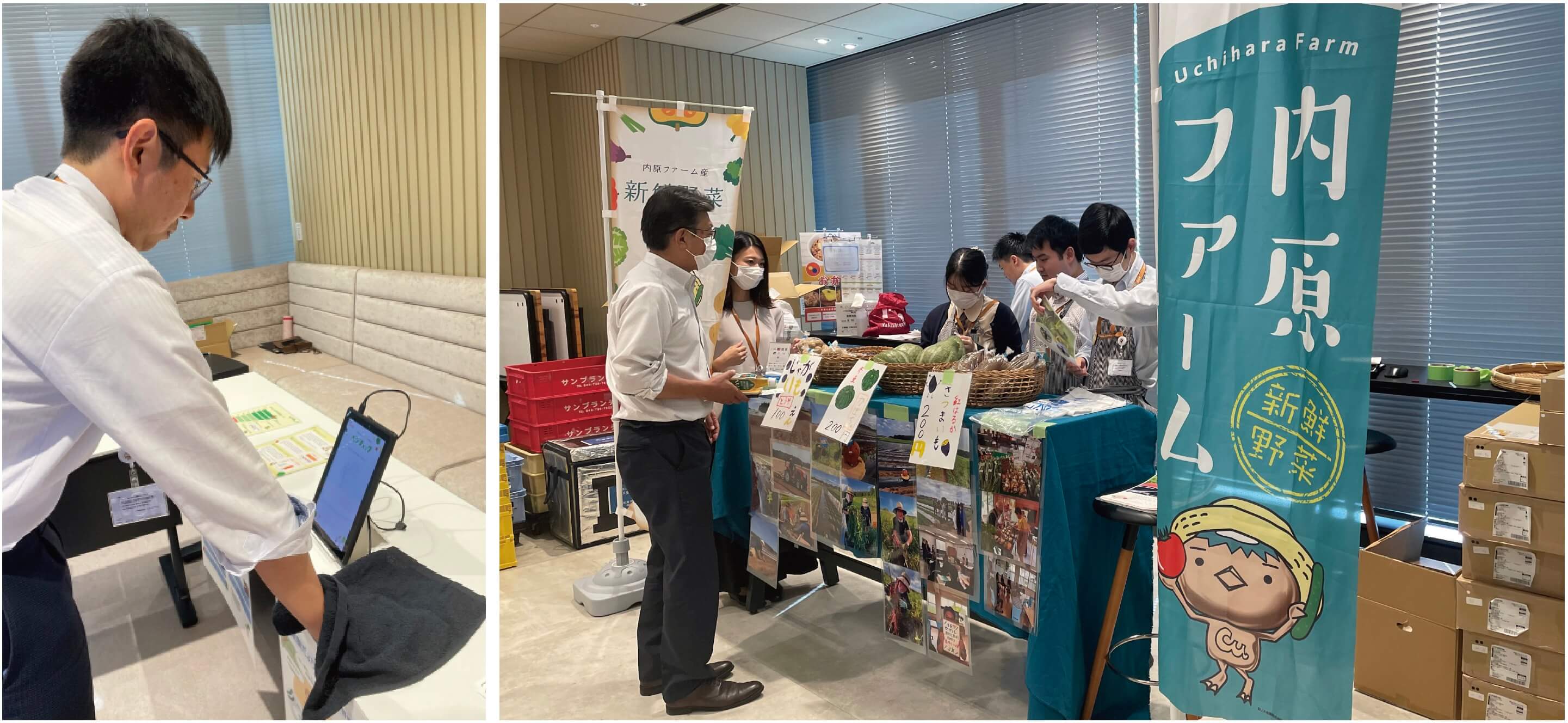
We are promoting a variety of measures to improve the mental and physical health of our employees through a project system in which all of our operating sites participate. In fiscal 2023, the Isohara Works, Hitachi Works, and Kurami Works assigned public health nurses and established health consultation offices. These efforts enabled the sites to utilize the health management support system more effectively, enabling centralized management of various health checkup results and working hour re-cords, and enabled significant progress in the development of industrial health systems.
Using the aforementioned system, we conducted physical fitness tests to determine current muscle strength, flexibility, sense of balance, etc. We also implemented self-care follow-up training for new employees as a mental health measure and improved workplaces based on the results of stress check group analysis. As a new initiative to reduce BMI, we also held a VegeCheck® event to encourage participants to measure their own vegetable intake. A large number of employees participated in the event, through which we raised awareness of the need to improve dietary habits by providing participants with vegetables harvested at Uchihara Farms and offering vegetable juice tastings.